Development of Semi-automatic Murukku Extruder
Abstract
Murukku is a delicious south Indian snack product prepared at household level as evening snack and also during festival seasons. The developed semi-automatic murukku extruder comprised of electric motor, power transmission system, a self-reversing screw rod, dough barrel and piston, die, and collection tray. The performance evaluation of extruder was done under three different moisture content of dough viz., 24%; 25%; and 26% respectively, and also at three different speed of self-reversing screw rod viz.,18 rpm; 15 rpm; and 12 rpm respectively. The statistical evaluation of extruder efficiency and sensory evaluation of final product samples was done. The results indicated that the efficiency of murukku extruder was found maximum when the dough moisture is at 25% and the speed of self-reversing screw rod at 12 revolutions per minute.
Keywords
Extruder, Selfreversing screw rod, Dough, Piston, Murukku
INTRODUCTION
Small scale machines are cost-efficient and beneficial for small and marginal farmer. Extrusion is a process used to create objects of a fixed cross-sectional profile. A material is pushed through a die of the desired cross-section. Food extrusion is a form of extrusion process and the same techniques used in food processing. It is a process by which a set of mixed ingredients are forced through an opening in a perforated plate or die (Harper, 1998) (Harper 1998) with a design specific to the food, and is then cut to a specified size.
Extrusion-technology is gaining increasing popularity in the global agro-food processing industry, particularly in the food sectors (Mensah & Tomkins, 2003) and (Singh, Singh, Sandhu, Bawa, & Sekhon, 1996). Fully automatic machines are available in the market to carry out this operation, but they are costly and involve complex machinery parts for which the maintenance cost is also comparatively high. Developing low-cost food processing equipment has got important in nowadays to encourage the entrepreneurs, who enter the business with less investment (Deo, Mathew, & Manikantan, 2020). Semi-automatic Murukku extruder has a greater advantage over a fully automatic one, in which diversified products can be extruded when needed, like idiappam, sevai, seeval, etc. A piston and cylinder type extruder that presses the dough through a die or orifice of definite shape which is operated by electric motor is known as Murukku extruder. The name derives from the Tamil word for "twisted" which refers to its shape. Murukku is popular all over India, and also in other countries where Tamil diaspora is present: Sri Lanka, Singapore and Malaysia.
Materials and Methods
Description of different parts
To develop the semi-automatic murukku extruder, different components were fabricated in the workshop and the materials selected are described in Table 1 . The fabrication of different parts of the extruser and design concepts are described below:
Main Frame : The main frame was manufactured using square pipe of stainless steel 304 grade materials (Figure 1 ). The dimesion of the main frame was 456x465x650 mm. The joints are welded together using Stainless steel arc-welding machine with the help of a 10-gauge stainless steel welding rod 304 grade. For facilitating the movement of machine 3-inch rotatable wheels are fixed to all the four legs of the main frame.
Sub-Frame:The sub frame was made using a metal channel of mild steel material (Figure 1 ). The length of frame height is fixed as 660 mm. And the bottom plate of dimensions 335 mm X 75 mm was fixed to the sub-frame using arc welding with the help of 10-gauge mild steel welding rod. The sub frame was attached to the main frame by joining the bottom plate and main frame through 10mm holes and fastened bolt and nut.
S upporting plates and Bushes : Supporting plates were made using mild steel metal plates of dimensions 325mm X 80mm (Figure 2 ). At the center of supporting plate 1, a bore of diameter 49mm was created using lathe machine for the movement of screw rod, and four holes of diameter 10mm was created using a drilling machine at the corners of plates in order to joining it with the angle which was welded to the sub-frame and four holes of diameter 10mm was created using a drilling machine at the corners of plates in order to joining it with the angle which was welded to the sub-frame. And each plate is joined to the angle through the holes of diameter 10mm and fastened using bolt and nut. The dimension of the supporting plates and bushes are shown in Table 2.
S No |
Extruder parts |
Material Selected for Extruder parts |
1. |
Main Frame |
304 food grade Stainless steel |
2. |
Sub-frame |
Mild Steel |
3. |
Supporting plates & bushes |
Mild Steel |
4. |
Self-reversing screw rod |
EN-8 grade Mild steel |
5. |
Reversing nut |
EN-8 grade Mild steel |
6. |
Driver pulley |
Cast-iron |
7. |
Worm gear assembly |
Aluminum |
8. |
Electric motor |
Cast-iron |
9. |
Dough barrel |
304 food grade Stainless steel |
10. |
Piston |
304 food grade Stainless steel |
11. |
Die / orifice |
304 food grade Stainless steel |
12. |
Dough Collection tray |
304 food grade Stainless steel |
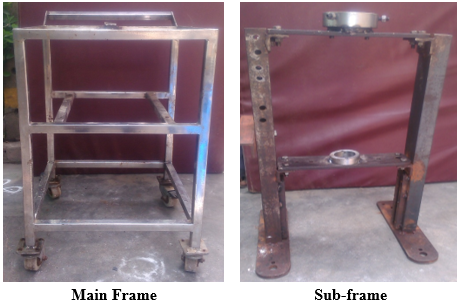
Self-Reversing Screw Rod : The Self – reversing screw rod was manufactured using EN-8 grade mild steel metal rod in a lathe machine. Its length was 360 mm while the diameter was 49 mm (Figure 3 ). The depth, width and pitch of screw thread was 4mm, 4mm, 12.7 mm, respectively. The length of the plain part of the rod was 340 mm with diameter of 40 mm.
Reversing Nut : The reversing nut was manufactured using mild steel metal in a lathe machine. Its length and thickness were 40mm and 3.8 mm, respectively. And this reversing nut assembly was joined to the supporting plate 1, through an angle which having hole of dimension 10mm diameter and fastened to the plate hole using bolt and nut.
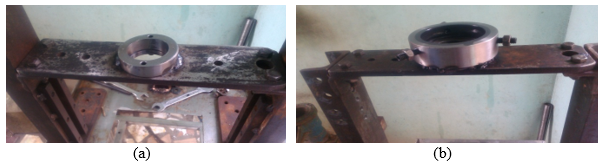
S.No. |
Holes dimensions of plates |
Dimensions for Supporting bush 1 (mm) |
Dimensions for Supporting bush 2 (mm) |
1. |
Outer diameter |
75 |
110 |
2. |
Inner diameter |
49 |
40 |
3. |
Thickness |
25 |
30 |
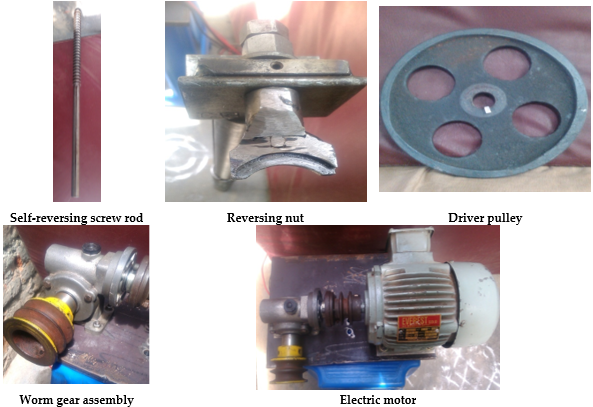
Driver pulley : The driver pulley is one of the components of power transmission system of the extruder. It was made up of cast iron material and the dimensions of the driver pulley are mentioned in the table below. The diameter and bore of the driver pully were 356 and 40 mm, respectively. The dimension of the keyway was 34mm x9mm x 4.5 mm. And this pulley was fitted to the supporting bush 2 in the bore made for it of dimension 80mm diameter and fastened by Allen key.
Worm Gear Assembly : A worm gear assembly of 25:1 ratio was coupled to the power source (electric motor), for the purpose for reducing the speed of the rotation (Figure 3 ). The input and output shaft diameter were 15mm and 19 mm. the pitch of the worm teeth was 15mm.
Electric Motor : Electric motor was the power source of the extruder; the body of motor was made of cast iron material and fitted to the sub frame through the metal plate which was welded to the sub-frame. The specifications of selected electric motor are given in the Table 3 .
S.No. |
Part of electric motor |
Units |
1. |
Power |
1 HP |
2. |
Speed |
1440 rpm |
3. |
Phase |
3 |
4. |
Ampere |
2 |
5. |
Shaft diameter |
19 mm |
The power source (electric motor) is coupled to the power transmission system component (worm gear assembly), through a flange which is fastened by Allen key.
Dough Barrel : The dough barrel was made of 304 grade stainless steel material; the box shape was attained by shearing the Stainless-Steel sheet. The dimensions of dough barrel were 200mm x200 mmx 200 mm and thickness of 1.5 mm.
Piston: The piston was made of 304 grade stainless steel metal; it is fitted to the self-reversing screw rod by welding it to a metal bush which was already fitted to the screw rod. The length and height were 200m and 215 mm, respectively.
Die: The die was made of 304 grade stainless steel metal sheets. Perforations on the die were created using single punching perforating machine. Its dimension was 195mm x195mm x1.5 mm.
Dough Collection Tray : The dough collection was made using 304 grade stainless steel material, the collection tray was fitted to the handle by welding of 304 grade stainless steel welding rod.
RESULTS AND DISCUSSION
This Semi-automatic murukku extruder (Figure 4) was working on the principle of mechanical extrusion process (Jansen & Harper, 1980), in which the dough was filled in a barrel and pressed over by a piston and conveyed through a die or orifice of definite shape to the collecting tray. The "up" and "down" movement of the piston is governed by self- reversing screw rod driven by an electric motor which was
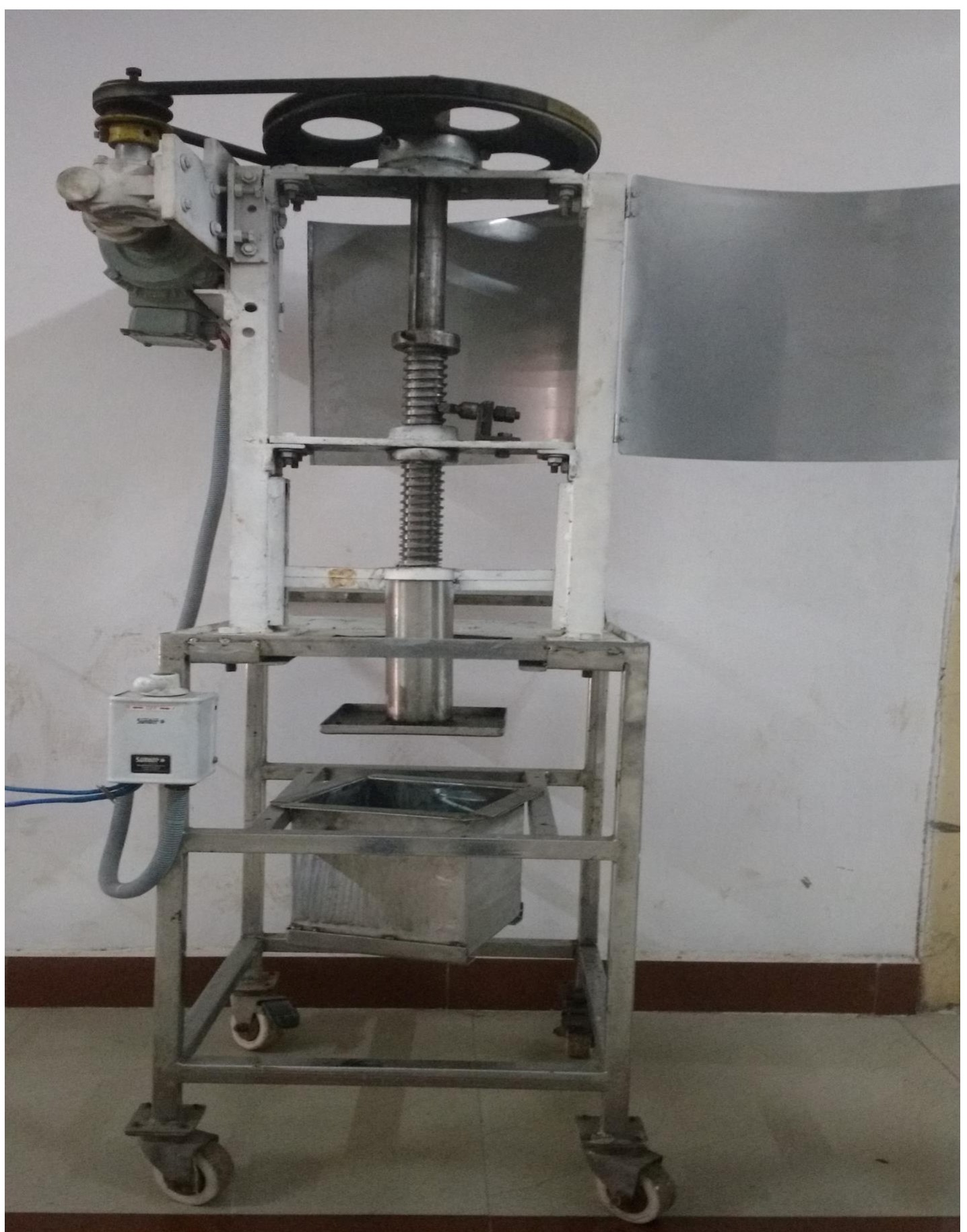
S. No. |
Ingredients |
Quantity (grams) |
1. |
Rice flour |
650 |
2. |
Black gram |
250 |
3. |
Salt |
25 |
4. |
Spices, Condiments, and processing aids |
75 |
Preparation of Dough
The optimum quality raw materials were selected and used for dough preparation. Rice flour was sieved for uniform mixing. Likewise, Black gram flour was also sieved. The flours were added together and salt, spices and condiment were added. This flour formulation was kneaded together by adding 200 ml of water; the water was added in small quantities at uniform interval for uniform kneading.
Speed of Self Reversing Screw Rod
Based on the preliminary tests performed, the screw speed at three different diameters of driver pulley and belt, when speed of motor at 1440 rpm coupled to a worm gear assembly of ratio 25:1 (Table 5).
Diameter of the Driving Pulley (inches) |
Diameter of Driving belt (inches) |
Speed of the Self reversing Screw Rod (rpm) |
10 |
46 |
18 |
12 |
48 |
15 |
14 |
50 |
12 |
As per the results, maximum speed of the screw was achieved when the self-reversing screw rod is connected to the driver pulley and belt of diameter 10 inch and 46 inches respectively. And minimum speed of the screw was achieved when the self-reversing screw rod is connected to the driver pulley and belt of diameter 14 inch and 50 inches respectively.
Sensory Analysis
Based on the average scores given by the judging panelists, the murukku prepared by extrusion process using the developed murukku extruder were within the acceptable range while, the murukku prepared when dough moisture is maintained at 25%, and the speed of self-reversing screw rod is maintained at 12 revolutions per minute has got significantly better scores which are given in the table below. The sensory analysis was conducted (Meilgaard, Civille, & Carr, 1999) with a panel of 25 members of College of Food and Dairy Technology, TANUVAS, Chennai. The panel members are provided with murukku samples prepared after extrusion by a developed extruder, and evaluated for the organoleptic characteristics viz., appearance, color, taste, flavor, texture, crispiness and overall acceptability.
S. No. |
Sensory attribute |
Score |
1 |
Appearance |
7.8±0.005 |
2 |
Colour |
7.9±0.06 |
3 |
Flavor |
7.8±0.03 |
4 |
Texture |
8.7±0.01 |
5 |
crispiness |
8.3±0.01 |
6 |
Taste |
8.5±0.02 |
7 |
Overall acceptability |
8.6±0.06 |
Performance Evaluation Technique
Table 7 shows the mean value found after three trails of extrusion at three different speeds S1, S2, S3 and three different moisture M1, M2, M3.
Trails |
Mean values of Input (g) |
Mean values of Output (g) |
Mean values of Extruder Efficiency (%) |
S1 M1 |
1190 |
1055 |
88.65 |
S2 M1 |
1190 |
1062 |
89.24 |
S3 M1 |
1190 |
1067 |
89.66 |
S1 M2 |
1200 |
1132 |
94.33 |
S2 M2 |
1200 |
1146 |
95.50 |
S3 M2 |
1200 |
1166 |
97.16 |
S1 M3 |
1210 |
1132 |
93.55 |
S2 M3 |
1210 |
1136 |
93.88 |
S3 M3 |
1210 |
1141 |
94.29 |
|
|
Mean |
92.91 |
Where,
S1 = Speed of pulley = 18rpm
S2 = Speed of pulley = 15rpm
S3 = Speed of pulley = 12rpm
M1 = Moisture content of dough = 24 % on wet basis
M2 = Moisture content of dough = 25 % on wet basis
M3 = Moisture content of dough = 26 % on wet basis
The extruder efficiency was found maximum as 97.16 %, when the screw speed was at 12 rpm and dough moisture was at 25 % on wet basis. The efficiency of extruder at three different dough moisture combination and three different screw speeds were calculated. And the mean data collected after three trails were taken for calculation of efficiency using the formula given below.
Efficiency of extruder at different dough moisture
Based on the analysis of the mean data collected for 24 % of dough moisture and the results were found. The maximum efficiency of extruder at dough moisture 24% is achieved when speed of the self-reversing screw maintained at 12 rpm. At dough moisture of 25% the maximum efficiency of extruder is achieved at 12 rpm of the self-reversing screw (Table 8). Based on the statistical analysis of the mean data collected after three trails of extrusion at dough moisture 26%, the maximum efficiency of extruder is achieved when speed of the self-reversing screw maintained at 12 rpm.
Speed of the Screw Rod (rpm) |
Efficiency of extruder (%) |
||
Moisture content |
|||
24 % |
25 % |
26 % |
|
18 |
88.65 |
94.33 |
93.55 |
15 |
89.24 |
95.50 |
93.88 |
12 |
89.66 |
97.16 |
94.29 |
Conclusion
Traditional snacks have become more popular and highly demanded snack product, nowadays, murukku is one among such snacks. For production of murukku in a large scale, dough extruder type should be facilitated and have to be implemented in a processing unit to minimize the production time with maximization of product production. Thus, in order to fulfill these demands, and at the same time to encourage and boost up the new entrepreneurs who enters the business with relatively less investment, this low cost semi-automatic murukku extruder was successfully developed. The results of statistical analysis show, the developed extruder will perform in its maximum efficiency when the dough moisture content was maintained at 25% and the Speed of self-reversing screw was maintained at 12 revolutions per minute.